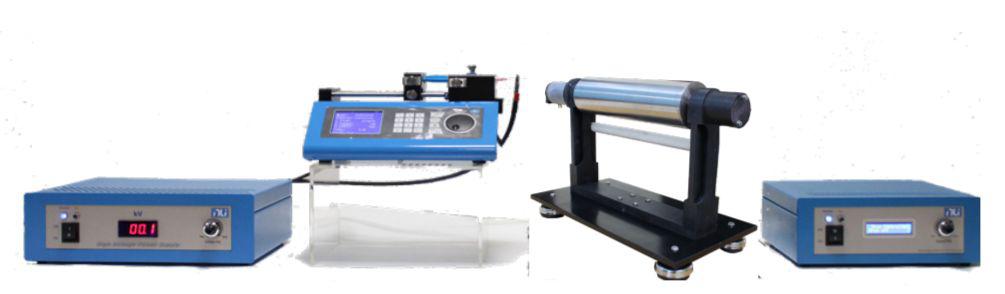
Electrospinning is a versatile and revolutionary technique for producing nanofibers used in applications ranging from filtration and tissue engineering to drug delivery and energy storage. The success of an electrospinning process heavily depends on the equipment used, making it essential to understand its key features and best practices. This guide delves into the critical components of electrospinning equipment, factors to consider when choosing a setup, and best practices for achieving optimal results.
Key Components of Electrospinning Equipment
Electrospinning equipment typically includes a high-voltage power supply, a syringe pump, a spinneret, and a collector. Each component plays a vital role in ensuring a consistent and efficient electrospinning process.
1. High-Voltage Power Supply
The power supply is the heart of the electrospinning system. It generates the electric field needed to draw fibers from the polymer solution. Voltage levels usually range between 10 kV and 50 kV, depending on the material and process parameters. Key considerations for the power supply include:
- Voltage Range: Choose equipment that supports the voltage requirements of your application.
- Stability: A stable electric field is crucial for uniform fiber formation.
- Safety Features: Look for built-in safety measures, such as overload protection, to ensure operator safety.
2. Syringe Pump
The syringe pump controls the flow rate of the polymer solution. Precise control over the flow rate ensures consistent fiber diameter and morphology. Important factors to consider include:
- Flow Rate Accuracy: High-precision pumps help achieve reproducible results.
- Compatibility: Ensure the pump can accommodate syringes of different sizes for versatility.
- Programmability: Advanced pumps allow for customizable flow rate profiles.
3. Spinneret
The spinneret (or nozzle) is where the polymer solution is ejected. Spinnerets come in various designs, including single-needle and multi-needle configurations. Features to consider include:
- Material: Stainless steel and polymer-coated nozzles resist corrosion and wear.
- Geometry: The nozzle shape affects fiber alignment and production efficiency.
- Customization: Some setups allow for interchangeable nozzles to produce specialized fiber structures.
4. Collector
The collector captures the electrospun fibers. Its design influences the fiber alignment and pattern. Common types of collectors include:
- Flat Collectors: Ideal for creating non-woven mats.
- Rotating Drums: Used for aligned fibers.
- Customized Designs: Specialized collectors enable unique fiber architectures for advanced applications.
Advanced Features in Modern Electrospinning Equipment
Innovations in electrospinning technology have introduced features that enhance productivity, precision, and safety.
1. Automation and Programmability
Modern systems often include automated controls for parameters such as voltage, flow rate, and environmental conditions. Programmable settings enable repeatable and efficient production.
2. Environmental Controls
Humidity and temperature significantly impact fiber morphology. Advanced setups include environmental chambers to maintain optimal conditions for specific polymers.
3. Multi-Jet Systems
For high-throughput applications, multi-jet electrospinning systems allow simultaneous production from multiple spinnerets, significantly increasing yield.
4. Real-Time Monitoring
Some systems are equipped with cameras and sensors to monitor the fiber formation process, allowing immediate adjustments to optimize quality.
Best Practices for Electrospinning
To maximize the efficiency and quality of the electrospinning process, it is essential to adhere to certain best practices.
1. Prepare the Polymer Solution Carefully
The quality of the polymer solution directly impacts the electrospinning process. Consider the following:
- Use a solvent that dissolves the polymer completely.
- Ensure the solution is free of impurities and air bubbles.
- Adjust parameters like viscosity and conductivity for optimal results.
2. Optimize Process Parameters
Fine-tuning the voltage, flow rate, and distance between the spinneret and collector is crucial. These parameters are interdependent, and small adjustments can significantly affect fiber quality.
3. Maintain Clean Equipment
Regular cleaning of the spinneret and other components prevents clogging and contamination, ensuring consistent fiber production.
4. Ensure Safety Measures
Electrospinning involves high-voltage electricity and potentially hazardous solvents. Implement safety protocols, such as wearing protective gear and ensuring proper ventilation.
5. Monitor Environmental Conditions
Control humidity and temperature to avoid defects like beading or fiber breakage. Using an environmental chamber can help maintain consistent conditions.
Choosing the Right Electrospinning Equipment
Selecting the appropriate equipment depends on your specific application and production needs. Here are some factors to consider:
- Application Requirements: Tailor the equipment features to your target application, such as medical devices, energy storage, or filtration.
- Scalability: Choose a system that can scale from laboratory research to industrial production.
- Budget: Balance advanced features with cost-effectiveness, considering the long-term benefits of automation and precision.
- Vendor Support: Opt for manufacturers that offer training, technical support, and maintenance services.
Conclusion
Electrospinning equipment forms the foundation for producing high-quality nanofibers. Understanding the key features of each component and adhering to best practices can significantly enhance the process’s efficiency and output. Whether you’re working on innovative medical textiles, advanced filtration systems, or cutting-edge energy devices, the right equipment and approach will pave the way for success.
Investing in modern, well-designed electrospinning systems not only improves fiber quality but also ensures reproducibility, scalability, and safety—key factors in staying competitive in today’s nanotechnology-driven industries.
0 Comments