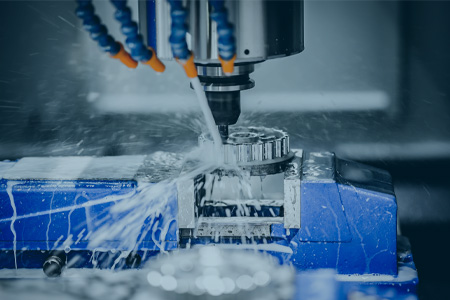
Precision machining plays a critical role in the oil and gas industry, ensuring the production of high-quality components that can withstand extreme operating conditions. The sector demands equipment and machinery that operate under high pressure, extreme temperatures, and corrosive environments. Oil and gas precision machining enables the creation of durable, accurate, and reliable parts that contribute to the efficiency and safety of drilling, extraction, transportation, and refining operations.
This article explores the importance of precision machining in oil and gas, the techniques used, key components produced, industry challenges, and emerging advancements that are shaping the future of manufacturing in this sector.
Why Precision Machining is Essential in Oil and Gas
Oil and gas operations rely on high-performance machinery and components that must meet exact specifications to function safely and efficiently. Precision machining ensures that parts are manufactured with tight tolerances, high strength, and excellent durability.
1. Enhanced Equipment Performance
The harsh environments of the oil and gas industry require machined components that can endure extreme conditions without failure. Precision machining ensures that every part meets strict dimensional accuracy, reducing wear and extending the lifespan of equipment.
2. Compliance with Industry Standards
Strict industry regulations, such as those set by the American Petroleum Institute (API) and the International Organization for Standardization (ISO), mandate that oil and gas components must meet specific safety and performance requirements. Precision machining ensures compliance with these standards, minimizing risks and ensuring operational efficiency.
3. Increased Operational Efficiency
By providing high-quality, accurately machined parts, precision machining reduces downtime, maintenance requirements, and operational failures. This leads to greater productivity and cost savings for oil and gas companies.
4. Customization for Unique Applications
Each oil and gas project has specific requirements, making custom machining solutions essential. Precision machining allows manufacturers to produce customized components that meet the exact needs of different drilling and extraction operations.
Precision Machining Techniques Used in Oil and Gas
Several advanced machining techniques are used to create high-quality components for the oil and gas industry. These methods ensure the accuracy, consistency, and durability of machined parts.
1. CNC Machining
Computer Numerical Control (CNC) machining is widely used for manufacturing complex, high-precision parts.
- CNC Turning: Used to create cylindrical components such as shafts and couplings.
- CNC Milling: Ideal for flat, contoured, and intricate components like valve bodies and pump housings.
2. Deep-Hole Drilling and Boring
Many oil and gas components require deep and precisely aligned holes for fluid transfer and pressure control.
- Gun drilling is used to create deep, straight holes with high accuracy.
- Boring operations help in refining hole diameters to meet precise tolerances.
3. Grinding and Honing
Precision grinding and honing processes help achieve ultra-tight tolerances and superior surface finishes, which are critical for components such as seals, pistons, and hydraulic parts.
4. Electrical Discharge Machining (EDM)
EDM is used for machining hard metals and intricate geometries, such as turbine blades and pressure control components.
5. Heat Treatment and Coating
To improve durability and resistance to corrosion and wear, machined components undergo heat treatment and specialized coatings such as ceramic or thermal barrier coatings.
Key Components Produced by Precision Machining
Precision machining is responsible for manufacturing critical components used in oil and gas exploration, drilling, extraction, refining, and transportation.
1. Drilling Equipment Components
- Drill bits for cutting through rock formations
- Drill collars that provide weight and stability
- Mud pumps for circulating drilling fluids
2. Flow Control and Pipeline Components
- Flanges and couplings for secure pipeline assembly
- Valves and seals to control oil and gas flow
- Manifolds for fluid distribution
3. Pumps and Compressors
- Pump impellers and casings for fluid movement
- Compressor blades and housings for gas processing
4. Pressure Control Systems
- Blowout preventers (BOPs) for preventing well blowouts
- Wellhead components for pressure regulation
5. Structural and Support Components
- Offshore platform components
- Subsea riser systems
- High-strength fasteners and bolts
Challenges in Oil and Gas Precision Machining
Despite its advantages, precision machining in the oil and gas industry presents several challenges that must be addressed to maintain efficiency and cost-effectiveness.
1. Machining Tough Materials
Oil and gas components are often made from superalloys such as Inconel, titanium, and stainless steel, which are difficult to machine due to their hardness and heat resistance.
2. Maintaining Tight Tolerances
The oil and gas industry requires precision parts with micron-level accuracy, making quality control a significant challenge.
3. Regulatory Compliance
Machined components must adhere to API, ISO, and ASME standards, requiring strict inspection and testing.
4. High Production Costs
Rising costs of raw materials, labor, and advanced machining equipment contribute to increased manufacturing expenses.
5. Supply Chain Disruptions
Global supply chain challenges, including material shortages and transportation delays, can impact production schedules and costs.
Emerging Trends in Oil and Gas Precision Machining
Technological advancements are transforming precision machining, making the manufacturing process more efficient, sustainable, and precise.
1. Automation and Robotics
Automated CNC machining and robotic systems improve speed, accuracy, and consistency, reducing labor costs and production time.
2. Additive Manufacturing (3D Printing)
3D printing enables rapid prototyping and the production of custom components, reducing waste and lead times.
3. Advanced Coatings for Wear Resistance
Innovative coatings, such as ceramic, diamond-like carbon (DLC), and thermal spray coatings, enhance the durability of machined parts.
4. IoT-Enabled Smart Machining
The integration of IoT sensors in machining tools allows real-time monitoring, predictive maintenance, and performance optimization.
5. Sustainable Machining Practices
Eco-friendly machining solutions, including energy-efficient machines, biodegradable cutting fluids, and material recycling, promote sustainability in the industry.
Conclusion
oil and gas precision machining is essential for producing high-quality, durable components used in exploration, drilling, refining, and transportation operations. Advanced machining techniques, such as CNC machining, deep-hole drilling, and EDM, ensure that parts meet strict industry standards and operational demands.
Despite challenges like machining tough materials, high costs, and strict compliance requirements, innovation in automation, IoT, and additive manufacturing is shaping the future of oil and gas machining. These advancements improve efficiency, reliability, and sustainability, ensuring that precision machining continues to play a vital role in the energy sector.
0 Comments